Global businesses like ours have a duty to reinvent the way they operate. If we act quicky and boldly, we can still lessen the worst of the expected impacts. That is why we are working hard to reduce our waste and our emissions, and continually seeking to implement measures that meaningfully cut our environmental footprint.
Discover more below about the three pillars of our sustainability strategy that focus on our planet: Greenhouse Gas Emissions; Conscious Materials; and Waste & Circularity.
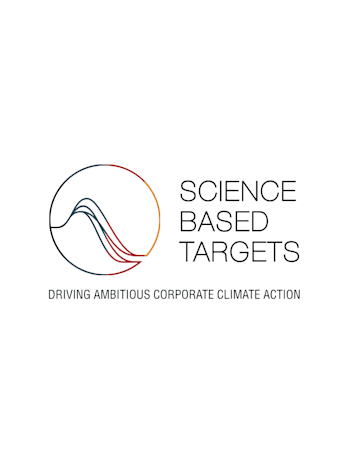
Snižování emisí
Title:Plány snížení rozsahu 1 a 2:
• Investice do naší energetické infrastruktury, včetně obnovitelných zdrojů energie, fotovoltaiky, tepelných čerpadel, vodíkové infrastruktury a potenciálu pro skladování energie s cílem dále zlepšit naši energetickou účinnost.
• Zavedení elektrifikace všude, kde je to možné, včetně našich pecí na tavení skla.
• Vyrovnávání zbývající spotřeby energie pomocí certifikátů energetických atributů pro obnovitelné zdroje.
Plány snížení rozsahu 3:
• Zvyšování efektivity zpracování materiálů našich výrobků a přechod od primárních k recyklovaným zdrojům kovů.
• Realizace globální hybridní pracovní politiky (včetně některých dnů práce z domova).
• Spolupráce s našimi dodavateli na podpoře využívání obnovitelných zdrojů energie v jejich výrobních procesech.
• Postupný přechod od letecké k námořní a železniční nákladní dopravě.
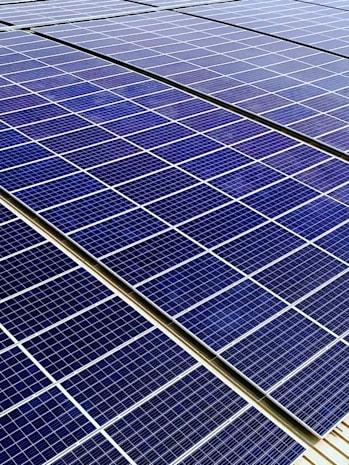
Energiezuinigheid
Title:Als onderdeel van onze maatregelen om onze energiezuinigheid te verhogen, onze uitstoot van broeikasgassen te verminderen en over te schakelen op hernieuwbare energiebronnen waar mogelijk, streven we ernaar om het gebruik van fotovoltaïsche systemen op onze productielocaties en administratiekantoren uit te breiden. In Wattens in Oostenrijk hebben we ons tweede grootschalige fotovoltaïsche systeem geïnstalleerd dat 300 wattpiek (Wp) biedt en 1600 m2 omvat. We hebben eerder een systeem van 1400 Wp geïnstalleerd op onze productielocatie in Thailand evenals een warmwatersysteem op zonne-energie op het dak in India, en er staan verschillende fotovoltaïsche systemen op de planning.
Ontwerpstudie voor glassmeltovens
We zijn samen met een multinationaal glasbedrijf dat zich specialiseert in glas en glaskeramiek een ontwerpstudie gestart om te testen of onze aggregaten uitsluitend aan de hand van elektriciteit gesmolten kunnen worden. Uit de studie bleek dat de aggregaten gesmolten kunnen worden door 90% elektriciteit te gebruiken, wat betekent dat we het gebruik van gas tijdens dit proces aanzienlijk kunnen verminderen. We kunnen bijna een concept implementeren waarmee we de resterende 10% van de verbruikte energie kunnen aanpakken. Zodra we dit bereikt hebben, kunnen we grote hoeveelheden aggregaten smelten met behulp van 100% hernieuwbare energie, een grote mijlpaal in ons streven om de koolstofvoetafdruk van ons kristal te verminderen.
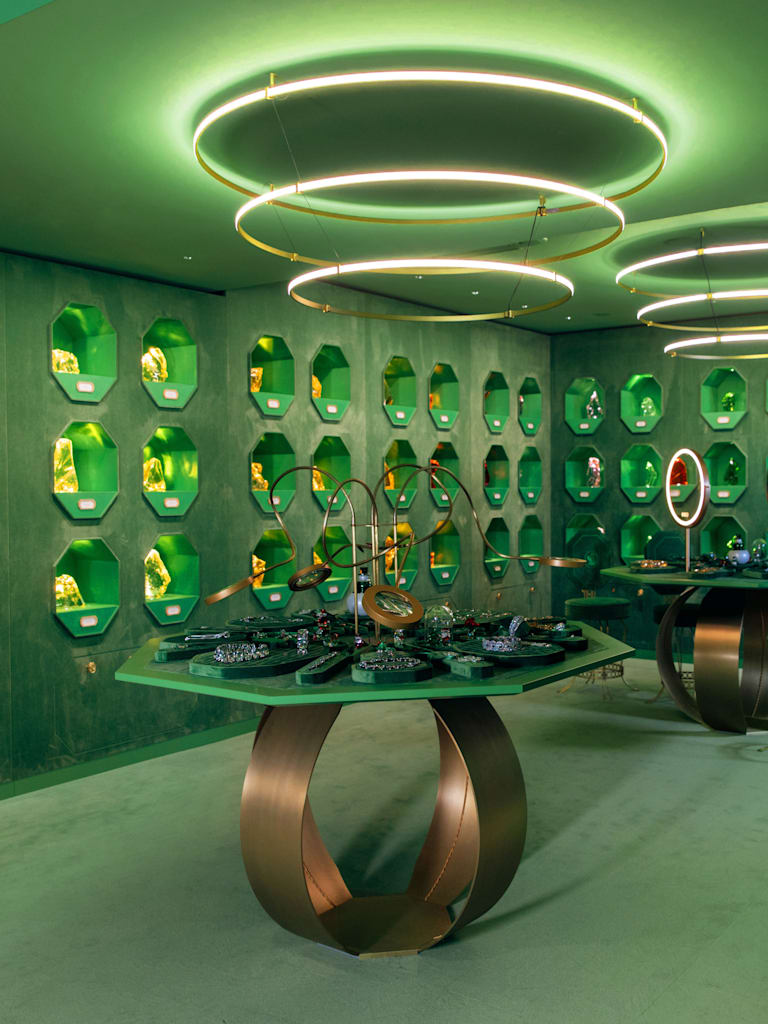
Swarovski stores
Title:Hoewel er veel aandacht wordt besteed aan de bouwmaterialen van stores en hun energieverbruik, is de focus op de aanzienlijke hoeveelheden afvalmateriaal die worden geproduceerd bij de verhuizingen, sluitingen en verbouwingen van stores een stuk lager. We hebben meerdere experimenten uitgevoerd om te bepalen of eerdere elementen van onze store-architectuur gerecycled kunnen worden en hebben tot nu toe meer dan 100 metrische ton aan materiaal via onze commerciële partners gerecycled. We zijn ervan overtuigd dat het onze verantwoordelijkheid is om verantwoord te handelen aan het einde van de levensduur van stores en niet alleen vóór de grote opening of tijdens dagelijkse werkzaamheden.
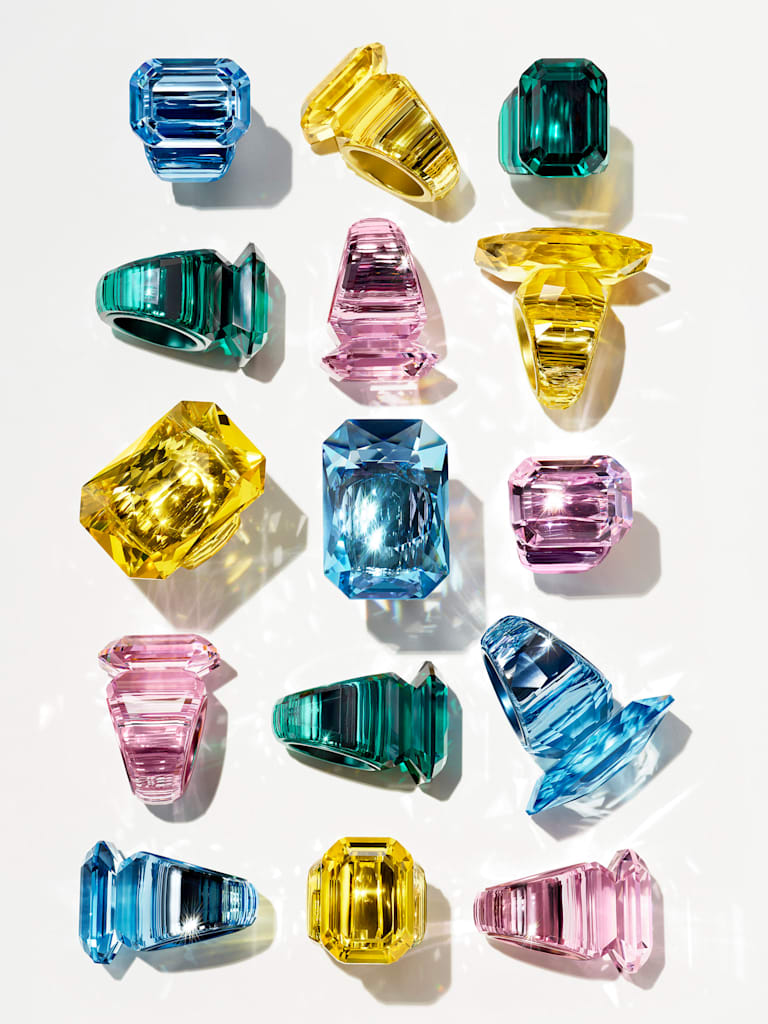
Produtos sustentáveis
Title:Mandatámos que, até 2030, 50% dos nossos produtos devem ser criados em conformidade com os nossos Princípios Orientadores de Produtos Sustentáveis.
• Os materiais são derivados de fontes geridas ou recicladas de forma responsável.
• Os produtos são produzidos eficientemente, sem desperdícios, e podem ser alvo de outro fim.
• Os clientes podem facilmente devolver os artigos usados para que possamos extrair os respetivos materiais preciosos.
• Os produtos não prejudicam as pessoas nem o ambiente.
• As comunicações em termos dos produtos são honestas, éticas e promovem uma utilização responsável.
Para nos ajudar a atingir este objetivo desafiante, lançámos em 2021 a nossa Conduta de Materiais Sustentáveis (SMP). A SMP permite que as nossas equipas de Design, Desenvolvimento de Produto, Marketing de Produto e Operações trabalhem em colaboração para introduzir materiais mais sustentáveis. Além disso, fornece-nos as ferramentas para avaliar os atributos de sustentabilidade dos materiais desde o início do processo.
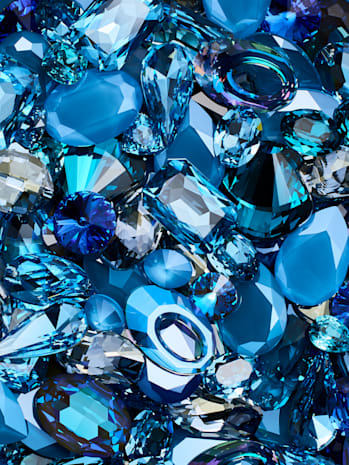
Cristalli rinati
Title:Crediamo nel potere positivo e trasformativo della collaborazione e, attraverso i nostri progetti di design consapevole e le nostre partnership, doniamo cristalli rinati ad istituzioni accademiche di fama mondiale, a designer emergenti e a nomi affermati sulla scena internazionale perché li utilizzino nelle loro creazioni. Lo nostro intento è di incoraggiarli a utilizzare questo squisito materiale in modo creativo, oltre ad aumentare la consapevolezza dell’importanza del design sostenibile e degli scarti come risorsa preziosa.
Nel 2021 abbiamo collaborato con Viktor&Rolf, che hanno integrato cristalli rinati nella loro collezione di Haute Couture Autunno/Inverno 2021, e con Kevin Germanier, che ha realizzato la sua collezione Primavera/Estate 2022 utilizzando cristalli rinati e materiali sostenibili. Abbiamo anche collaborato con Germanier per la realizzazione di un flacone di profumo in materiale riciclato, tempestato di cristalli rinati, per Guerlain.
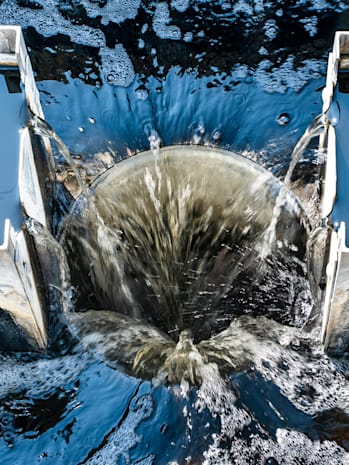
Efficienze nella produzione
Title:Nel nostro stabilimento di produzione, anch’esso situato a Wattens, utilizziamo un circuito lubrificante di refrigerazione come ausilio nel taglio dei cristalli. Il circuito contiene 1.200 m3 di liquido e richiede l’aggiunta attenta di varie sostanze chimiche per garantire prestazioni ottimali e stabilità. Dal 2015 al 2021, abbiamo dimezzato la quantità di lubrificante di refrigerazione utilizzato. Inoltre, siamo anche riusciti a eliminare completamente o parzialmente dal processo una serie di sostanze chimiche, compreso il nostro kit di agenti precipitanti e antischiuma, e abbiamo rinnovato il nostro inibitore della corrosione allo scopo di eliminare il fosforo
Tutti questi miglioramenti sono il risultato di innovazione piuttosto che di una minore produzione e presentano anche vantaggi in termini di sicurezza per i nostri colleghi.